The rise of digital twins in industrial applications
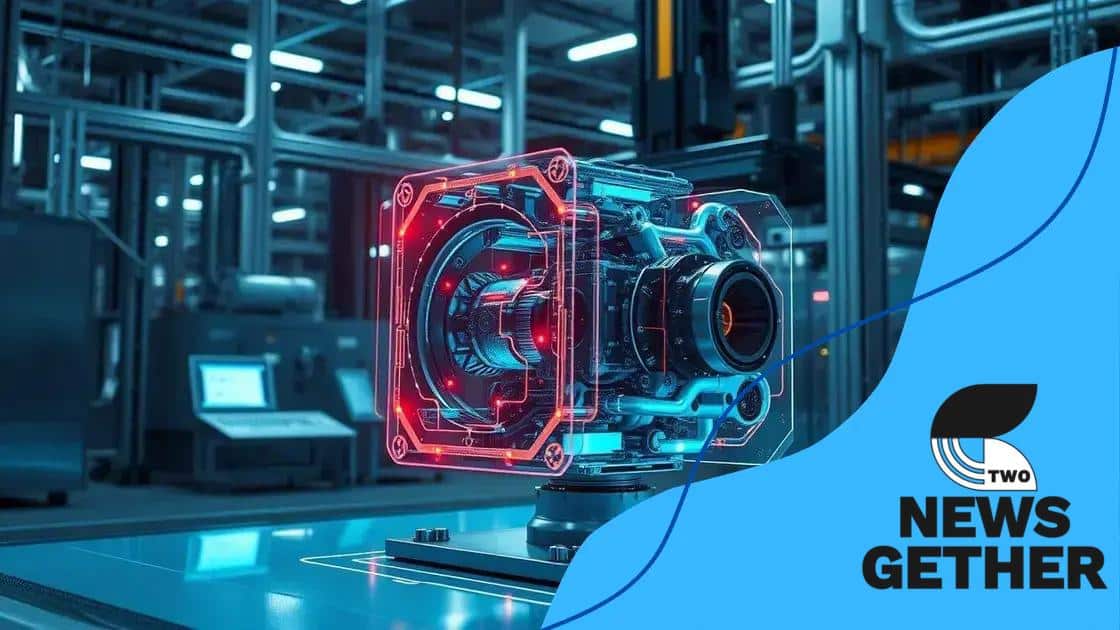
The rise of digital twins in industrial applications enhances efficiency, predictive maintenance, and data-driven decision-making by creating virtual models that simulate real-world systems.
The rise of digital twins in industrial applications is transforming how businesses operate. Ever wondered how this technology can improve efficiency and innovation in various sectors? Let’s dive into the fascinating world of digital twins.
Understanding digital twins: definitions and concepts
Understanding digital twins is key to leveraging this groundbreaking technology in various industries. A digital twin is a virtual replica of a physical object or system, used to analyze and optimize performance. By simulating real-world conditions, companies can gain valuable insights into operations.
Key Characteristics of Digital Twins
There are several defining traits of digital twins that set them apart from other technologies:
- Real-time data: Digital twins use sensors to obtain live data from their physical counterparts.
- Predictive analytics: They analyze data to forecast outcomes and identify potential issues before they arise.
- Continuous improvement: Digital twins evolve as new data becomes available, allowing for ongoing optimization.
This technology helps businesses make informed decisions, improve efficiency, and reduce costs. By creating a digital twin, industries can visualize processes, track performance, and quickly identify areas for enhancement. Furthermore, the integration of digital twins with other technologies, such as IoT, amplifies their potential, offering even deeper insights into operational workflows.
Applications of Digital Twins
Digital twins are revolutionizing various sectors, including:
- Manufacturing: Monitoring machinery and predicting maintenance needs.
- Healthcare: Simulating patient outcomes and treatment plans.
- Urban planning: Creating virtual cities to analyze traffic flow and resource usage.
By harnessing the power of digital twins, organizations position themselves to respond proactively to challenges and seize opportunities in an ever-evolving landscape. Experimenting with this innovative technology could lead to significant advancements and competitive advantages.
The benefits of using digital twins in industry
The benefits of using digital twins in industry are substantial, providing companies with innovative ways to enhance operations. This technology allows businesses to optimize performance, predict outcomes, and make data-driven decisions effectively.
Enhancing Efficiency
One major advantage of digital twins is the ability to increase operational efficiency. By monitoring real-time data, companies can quickly identify inefficiencies and implement improvements. This leads to smoother workflows and better resource management.
- Reduced downtime: Anticipating equipment failures helps in scheduling timely maintenance.
- Streamlined processes: Continuous monitoring aids in optimizing production lines.
- Cost savings: Efficient operations lower operational costs and increase profitability.
Furthermore, digital twins enable effective simulations. Businesses can test different scenarios without risking disruption to actual operations. This flexibility allows for experimenting with changes and understanding their potential impacts before implementation.
Improving Decision-Making
Another significant benefit of digital twins is improved decision-making. With access to real-time analytics and predictive insights, executives can make informed choices that drive growth. Enhanced visibility into operations and outcomes ensures that strategies are based on data rather than assumptions.
- Data-driven strategies: Analyze outcomes to shape future initiatives.
- Risk management: Identify potential risks early and create mitigation strategies.
- Customer satisfaction: Improved efficiency leads to faster service and better quality.
Ultimately, investing in digital twins pays off by fostering innovation and responsiveness. This technology helps industries keep up with market changes and customer demands, ensuring competitive advantages in a rapidly evolving landscape.
Case studies: successful applications of digital twins
Case studies on successful applications of digital twins highlight how various industries leverage this technology for transformative outcomes. Many sectors have adopted digital twins to optimize efficiency and drive innovation.
Aerospace Innovations
One prominent example is in the aerospace industry, where companies like Boeing use digital twins to enhance aircraft design and maintenance. By simulating aircraft behavior in different conditions, engineers can predict how changes affect performance. This approach helps in proactive maintenance, which significantly reduces operational costs.
- Predictive maintenance: Early identification of potential issues.
- Design optimization: Testing prototypes virtually before physical creation.
- Operational efficiency: Streamlined processes increase production speed.
Additionally, the aerospace sector benefits from reduced time-to-market for new aircraft models, allowing companies to remain competitive.
Manufacturing Excellence
In the manufacturing sector, General Electric (GE) employs digital twins for their gas turbines. By creating digital models of turbines, GE engineers monitor performance in real time. This technological integration allows for
- Condition monitoring: Accurate tracking of turbine health.
- Enhanced diagnostics: Identifying performance issues before they escalate.
- Efficiency improvements: Optimizing fuel consumption in real time.
Such applications have led to significant improvements in overall efficiency and reduced downtime.
Smart Cities and Urban Planning
Digital twins are not limited to manufacturing and aerospace; they also find their place in urban development. Cities like Singapore use digital twins to model urban environments. This innovation aids in planning infrastructure and managing resources effectively.
By modeling traffic flow and public transport systems, planners can design more efficient solutions that minimize congestion. This proactive approach contributes to sustainable growth and improved quality of life for residents.
With numerous industries reaping the benefits of digital twins, it becomes clear that this technology will continue to shape the future of business and urban development.
Challenges in implementing digital twins
Implementing digital twins presents various challenges that organizations must navigate. While the benefits of this technology are clear, hurdles can arise during integration and maintenance.
Data Management Issues
A significant challenge is managing the vast amounts of data that digital twins require. Accurate and timely data is essential for effective simulations. Organizations must invest in robust data collection and management systems. This includes:
- Data accuracy: Ensuring that real-time data is reliable and precise.
- Data integration: Combining data from multiple sources into a cohesive system.
- Storage solutions: Implementing systems that can handle large data volumes without losing performance.
Without proper data management, the simulations produced by digital twins may lead to incorrect conclusions, affecting decision-making.
Technical Complexity
The technical complexity of developing and maintaining digital twins can also pose challenges. Organizations may need specialized skills to build and operate these models effectively. This complexity can lead to:
- Skill gaps: Difficulty in finding qualified personnel with the necessary expertise.
- High costs: Expensive software and training programs may be necessary.
- System compatibility: Ensuring that existing systems can integrate with digital twin technologies.
Furthermore, organizations must ensure that they have the suitable infrastructure to support digital twins, which may require significant investments.
Change Management
Lastly, change management is a critical aspect when integrating digital twins into existing workflows. Employees may resist adopting new technologies. Therefore, companies need to foster a culture of innovation and adaptability. Key strategies include:
- Training programs: Providing comprehensive training to help employees understand the benefits and functionalities of digital twins.
- Communication: Clearly explaining the reasons behind implementing this technology.
- Support systems: Establishing support for employees to address concerns and questions.
By understanding these challenges, organizations can develop strategies to overcome them and fully harness the potential of digital twins.
Future trends for digital twins in industrial settings
Future trends for digital twins in industrial settings are set to redefine how businesses operate and innovate. As technology advances, digital twins will become increasingly integral to various industries. Companies are exploring new ways to leverage this technology, pushing boundaries beyond traditional applications.
Integration with AI and Machine Learning
One prominent trend is the integration of digital twins with artificial intelligence (AI) and machine learning. This combination will enhance predictive analytics, allowing businesses to foresee potential issues and opportunities more accurately. With AI capabilities, digital twins can analyze data patterns, making recommendations for optimizations.
- Automated insights: AI can provide real-time insights from the data collected by digital twins.
- Enhanced simulations: Machine learning algorithms can improve model accuracy over time.
- Proactive problem-solving: Anticipating maintenance needs before problems arise.
This evolution will enable organizations to be more agile and responsive to changes in the market.
Greater Adoption in Smart Manufacturing
Additionally, the adoption of digital twins in smart manufacturing will continue to expand. Factories are becoming increasingly automated, leading to more complex systems that require efficient management. Digital twins will play a vital role in this transition by providing insights into machinery and production processes.
These digital models will facilitate:
- Real-time monitoring: Allowing manufacturers to track performance continuously.
- Resource Optimization: Reducing waste and enhancing productivity.
- Rapid prototyping: Testing new product designs without physical prototypes.
The integration of digital twins with the Internet of Things (IoT) will further enhance this trend by providing a network of interconnected devices that share data seamlessly.
Impact on Product Development and Lifecycle Management
The future of digital twins also includes better product development and lifecycle management. By creating a digital twin of a product throughout its lifecycle, companies can gather valuable data from its design phase to its end-of-life. This holistic approach will lead to improved product quality and customer satisfaction.
Companies will be able to:
- Analyze performance: Understand how products perform in real-world situations.
- Facilitate feedback loops: Incorporate customer feedback into ongoing improvements.
- Sustainability goals: Enhance assessment of environmental impacts and promote sustainable practices.
As these trends unfold, the role of digital twins will become increasingly critical in shaping the future of industries.
FAQ – Frequently Asked Questions about Digital Twins in Industrial Applications
What are digital twins and how do they work?
Digital twins are virtual replicas of physical objects or systems that simulate real-world behavior using real-time data. They help analyze performance and optimize operations.
How can digital twins improve efficiency in industries?
Digital twins enhance efficiency by enabling real-time monitoring, predictive maintenance, and streamlined processes, leading to reduced downtime and improved productivity.
What role does AI play in digital twins?
AI enhances digital twins by providing predictive analytics and insights, allowing businesses to make data-driven decisions and anticipate issues before they arise.
What are the main challenges in implementing digital twins?
Challenges include data management issues, technical complexity, and change management, which organizations need to address to effectively use digital twins.